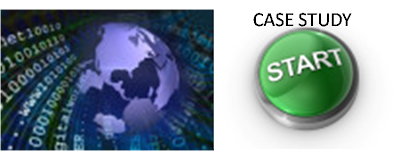
Create program to check all Purchasing and Logistics-related data requirements for large auto manufacturing plant. “Visual management”-compatible program required to easily evaluate the readiness status of all material for line-side adoption.
Initial Situation:
ERP system used by Purchasing and Logistics Department has numerous standard tools for use by responsible specialists to create, edit, view and monitor data related to the procurement and use of material for vehicle production. Each tool, however, only displays one small part of the information necessary to determine a material’s readiness for use in the vehicle.
Challenges and Goals:
1- Consolidate information from all ERP tools in one screen.
2- Provide easy “drill-down” capability to create any missing information.
3- Provide easy “drill-down” capability to edit existing data.
4- Automatically highlight missing data leading to production problems.
5- Automatically distribute responsibilities to each Purchasing
and Logistics specialist.
Approach:
1- Define complete data package before factory use of material
(from Purchasing and Logistics viewpoint).
2- Create a list of ERP system tools in use by the responsible specialists.
3- Form working group (composed of at least two “super-users” and consultant).
4- Layout the system using “Condition” diagrams.
5- Propose screen layouts containing each of the “procedure” boxes identified
in the condition diagram.
6- After agreement on output layout, program the application.
7- Document and train.
Benefits:
1- Increased user-friendliness of the system.
2- Improved specialist efficiency.
3- Improved monitoring.
4- Built in logic can detect potential problems before they impact production.
Considering that the average engineering change costs $50000 to implement and can affect hundreds or thousands of products, being able to detect production mistakes can save a company hundreds of thousands of dollars.
No comments:
Post a Comment